Cabinet Refinishing Sacramento is a surface-only refurbishment that does not change the function of your cabinets. It’s ideal if your wood cabinets are in good structural condition but have an outdated finish.
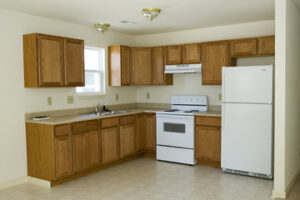
However, refinishing can be tricky—particularly when going from light to dark. It’s also typically not the best option if your doors and drawer fronts are made of thermofoil or laminate.
A key difference between cabinet refinishing and painting is that refinishing requires a full stripping process to remove the existing stain or paint from your cabinets. This can be done with a chemical stripper or sanding. Depending on the condition of your cabinets and the desired finish, either option may be appropriate for you.
While sanding is more time-consuming than simply cleaning your cabinets and applying a primer, it allows you to reach bare wood with minimal damage. If you are going to stain your cabinets, sanding is an essential step in the preparation process because it gives the wood a surface that will hold the stain well.
Paint can be used to cover blemishes on your cabinetry, but it is important to remember that paint will attract dust and dirt. You will need to wipe your painted cabinets down regularly to keep them clean and looking good.
When considering whether to refinish or repaint your cabinets, it is important to note that refinishing will likely cost more than simply repainting them. This is because refinishing includes the work necessary to get your cabinets back to their original state, which can be a lengthy process.
If you are unsure of which option is right for your project, talk to a professional. They can help you decide which will give you the best results for your budget and timeline. They can also address any structural or functional issues that you might be facing, such as broken knobs, misaligned doors, or other damage. They can even replace your hardware if it is beyond repair. If you are ready to discuss your options with a pro, enter your zip below and we’ll match you with top-rated pros.
Cleaning
Whether your cabinets are wood or laminate, they can get dirty over time. Dirt and grime build up on cabinet surfaces from cooking food, scrubbing dishes, and other daily activities. For most messes, a rag soaked in a mild soap solution should be enough to remove any residue and dirt on the surface.
For more stubborn grease stains, you may need to use a degreaser. Ideally, look for products that are non-toxic and formulated for laminates or painted surfaces. Avoid harsh chemicals such as white vinegar, chlorine bleach, abrasive cleansers and commercial citrus oil cleaners, which can damage the laminate or wood surface of your cabinets. If you do decide to use a stronger chemical, always test it on an inconspicuous area of your cabinets and follow the manufacturer’s instructions for safe and effective use.
If you notice a tough grease stain that just won’t budge, try a little baking soda mixed with water to create a paste and scrub the spot. If you still can’t remove the grease, you may need to try a more heavy-duty degreaser such as Murphy oil soap or Orange Cleaner. Always use these in a well-ventilated area, and be sure to wear gloves and follow the manufacturers’ instructions for safe and effective use.
Don’t forget to wipe the inside of your cabinets as well. Using a duster or cloth, spray the cleaning solution on your cabinet doors and wipe them clean, paying attention to any corners or crevices where dirt tends to collect. After rinsing your cabinets, be sure to dry them thoroughly to prevent water damage from excess moisture. Also, be sure to wipe down the cabinet hardware to remove any traces of the cleaner.
Primer
If you’ve talked to professional local painters or read painting blogs, chances are you’ve heard them talk about the importance of primer. But what is primer exactly? And do you really need to use it when painting your home?
Primer is an initial coating that’s applied to a surface before applying a coloured coat. It’s typically formulated to ensure that paint adheres to the surface, so using it can help prevent your new paint job from cracking or peeling. It also helps to protect the underlying material from moisture and mildew.
Different primers are available for indoor and outdoor use, so it’s important to choose the right one for your project. Interior primers are usually water-based and designed for drywall, while exterior primers are solvent-based and intended for wood surfaces. Some primers are stain-blocking, which can be useful if you’re covering a dark colour with a light one. It’s also worth noting that stain-blocking primers typically contain higher levels of volatile organic compounds (VOCs), so you’ll want to make sure you’re wearing a mask and properly venting your workspace while working with them.
You’ll need to let your primer dry completely before you apply the coloured coat. Depending on the product you’re using, this may take between 24 hours to two weeks. Some primers also require that the topcoat be applied within a specific time-frame to ensure optimal adhesion, so it’s important to check the label and follow the manufacturer’s instructions carefully. If you’re using a brush to apply your primer, be sure to smooth out any uneven spots or brush marks once it’s dried to prepare for the finish coat. And if you’re using a roller, be sure to use long, even strokes to avoid leaving any gaps or lines.
Paint
Cabinet paint is applied with a brush, roller or sprayer, and may require multiple coats to achieve the desired appearance. Care must be taken with any sanding between coats, and proper taping to avoid wall damage and drips. A high quality primer is used to ensure good adhesion and stain blocking properties. A low odor primer is ideal to allow homeowners to stay home during the project.
Paint can completely change the look of your cabinets, ranging from classic white or gray to bold colors that make a statement. Cabinets can also be glazed or distressed for added texture and depth to the design. Decorative trim and molding can be added to the cabinet doors and drawer fronts for further customization.
While refinishing is an excellent option for changing the overall look of your kitchen, it is not the best solution for addressing structural or functional issues such as warped cabinet doors or loose hardware. It is also not recommended for addressing minor cosmetic problems such as scratches or dings on the existing cabinet door or drawer front.
Refinishing is not as durable as refacing and can be easily damaged by moisture, dirt and grease. The process can be difficult for the average DIYer, and it is important to take the time to prepare the surface properly before beginning. If you decide to refinish your own cabinets, be sure to use a high quality primer, sand between coats, and carefully follow the manufacturers instructions for application. It is also helpful to label each cabinet door and drawer front before beginning, so that you can return them in the correct order once the refinishing is complete.
Finishing
Cabinet refinishing is a time-consuming process that involves chemical peels and extensive sanding. It is only a cosmetic improvement and does not address structural issues like warped doors or faulty hardware. Refinishing is typically only recommended when you want to change the color of your existing cabinet doors. Refinishing can be very difficult to complete if you have detailed cabinet door profiles, but it is often the best option if you are trying to make a large color change.
When choosing a cabinet paint, it’s important to choose a high-quality semi-gloss that can withstand a lot of wear and tear. The finish should be resistant to heat, water, mildew, scratches and dents. It is also critical to properly prep your cabinets before painting, including sanding and cleaning. The most effective way to apply a new coat of paint is with a professional spray gun, however you can use foam rollers and brushes as well.
Cabinet finishing techniques add dimension to your design and set your space apart from the rest. Omega offers several finishing options to optimize your style, including Antiquing and Vintage Touch. These techniques accentuate your wood by creating the look of natural wear on edges and profiles over time. These effects are lightly sanded over profiles, and include the appearance of worm holes, light dents and chiseling for a timeless feel.